In the world of logistics, efficient product management is crucial to the success of any operation. In this context, the distinction between compliant and non-compliant products plays a key role in ensuring quality and customer satisfaction.
Conforming product, what is it?
A conforming product is defined as one that meets all established requirements, both in terms of physical characteristics and associated documentation. This includes aspects such as:
- Technical specifications: The product must comply with the agreed dimensions, materials, functionalities and other technical characteristics.
- Packaging and labeling: Packaging should be adequate to protect the product during transportation and storage, and labeling should include all information required by law or regulation, such as product description, ingredients (in case of food), instructions for use and manufacturer's data.
- Transport and storage conditions: The product should be transported and stored in optimal conditions to preserve its integrity and quality.
- Legal and commercial documentation: The documentation associated with the product must be complete and correct, including invoices, certificates of origin, permits and any other documents required for its commercialization.
Compliance with these requirements ensures that the product received by the customer is as expected and meets the customer's needs.
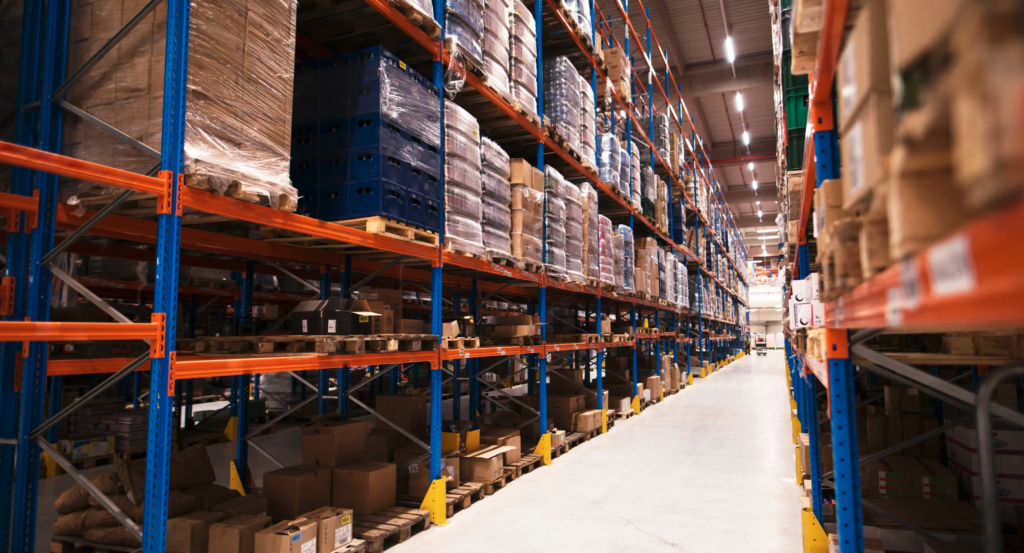
Non-conforming product
In contrast, a non-conforming product is one that presents some deviation or non-compliance with the established requirements. The causes of this nonconformity can be diverse, such as:
- Manufacturing defects: Errors in the production process that result in failed or damaged products.
- Damage during transport: Improper handling, accidents or adverse environmental conditions during transport may affect the integrity of the product.
- Faulty packaging: Poor packaging may not adequately protect the product, exposing it to damage or deterioration.
- Incorrect labeling: Errors in labeling information, such as product description, instructions for use or manufacturer's data, can lead to confusion or even risks for the consumer.
- Incomplete or incorrect documentation: The lack of essential information in the documentation associated with the product may hinder its commercialization or even generate legal problems.
How to manage non-conforming products?
The receipt of non-conforming products represents a problem for the company, since it implies additional costs for rework, returns, reshipments and possible compensation to the customer. In addition, it damages the company's image and can affect customer satisfaction.
Upon detection of a non-conforming product, it is essential to implement an adequate management process that allows:
- Identify the root cause of the nonconformity: It is crucial to investigate the causes that originated the problem to avoid its recurrence.
- Take corrective action: Actions should be implemented to correct the nonconforming product or replace it with a new one.
- Apply preventive actions: Measures should be implemented to prevent the nonconformity from recurring in the future.
- Communicate the situation to the customer: It is important to inform the customer about the situation in a clear and transparent manner, offering solutions and apologies for the inconvenience caused.
Effective nonconforming product management is an essential component of a robust quality management system in logistics. By minimizing the incidence of nonconforming products and properly managing the cases that do occur, companies can protect their reputation, reduce costs and ensure customer satisfaction.
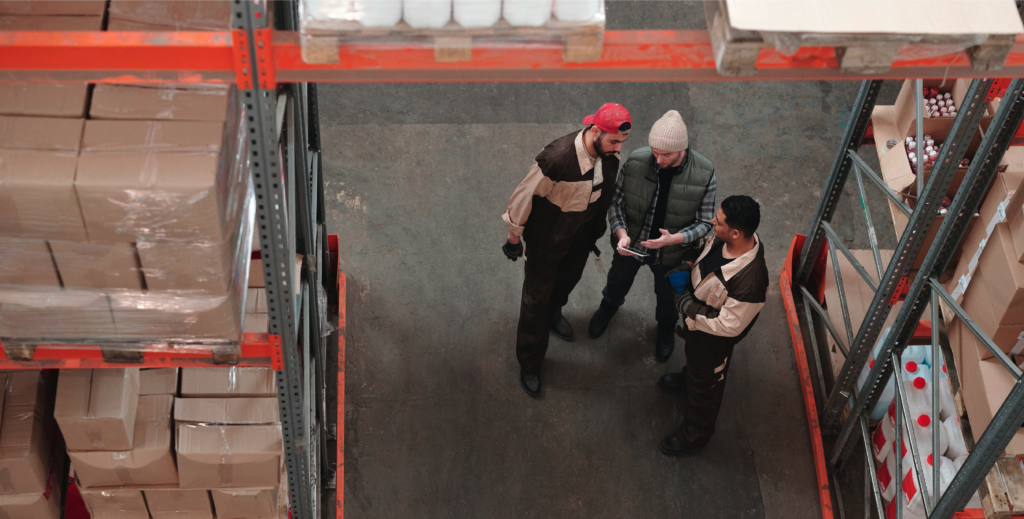
Key strategies for proper management of nonconforming products
Effective control of non-conforming products in a warehouse is crucial to optimize logistics operations, minimize losses and guarantee the quality of the final product delivered to the customer. As logistics experts, we can suggest these key strategies for proper handling of these products:
Identification and segregation:
- Establish a designated area: Designate a specific space within the warehouse for the exclusive storage of non-conforming products. This area should be signposted and have adequate conditions to protect the products and avoid mixing them with compliant products.
- Implement an identification system: Create a clear and efficient identification system for each nonconforming product. This may include physical labels, barcodes or distinctive markings that allow for quick traceability and tracking.
- Record information: Document in detail the relevant information for each nonconforming product, including date of receipt, product description, nature of the nonconformity, supplier and quantity of units affected.
2. Analysis and classification:
- Investigate root cause: Conduct a thorough investigation to determine the root cause of the nonconformance. This may involve physical inspections, laboratory analysis, review of production processes and communication with suppliers.
- Classify products: Classify nonconforming products according to the severity of the nonconformity and its potential impact on the customer. This classification may include categories such as "minor cosmetic defects", "functional defects" or "hazardous products".
- Prioritize action: Establish a prioritization system to determine the order in which nonconforming products will be addressed. Products that pose the greatest risk to customer safety or company image should be prioritized.
3. Decision making and corrective actions:
- Determine the final disposition: Based on the previous classification and analysis, make the appropriate decision on the final destination of each nonconforming product. Options may include:
- Remanufacturing: If possible and cost-effective, repair or remanufacture the product to meet quality standards.
- Scrapping: Destroy the product in a safe and responsible manner, following current environmental and safety standards.
- Price reduction: Sell the product at a reduced price, clearly informing the customer of the nature of the nonconformity.
- Return to supplier: Return the product to the original supplier for repair, replacement or refund, according to the terms agreed in the purchase contract.
- Implement corrective action: Take action to correct the root cause of the nonconformity and prevent its recurrence in the future. This may involve changes in production processes, staff training, supplier reviews or improvements in quality controls.
4. Documentation and registration:
- Maintain detailed records: Document all actions taken in relation to each nonconforming product, including date, action taken, responsible party and results obtained.
- Archive documentation: Store documentation in an organized and accessible manner for later consultation. This will allow trend analysis, identify patterns of nonconformity and take more effective preventive measures.
5. Communication and training:
- Communicate to stakeholders: Inform relevant personnel about the existence of nonconforming products, actions taken and lessons learned. This will foster transparency and collaboration to prevent future nonconformities.
- Train personnel: Provide training to warehouse personnel on procedures for identifying, segregating, analyzing and managing nonconforming products. This will ensure that all involved are familiar with their responsibilities and act consistently.
6. Continuous improvement:
- Analyze trends: Periodically review historical nonconforming product data to identify trends, patterns and areas of opportunity for improvement.
- Implement preventive actions: Develop and implement preventive actions based on trend analysis and lessons learned. This will help reduce the incidence of non-conforming products in the future.
- Review and update procedures: Periodically review and update nonconforming product control procedures to ensure that they conform to changing business needs and industry best practices.
By implementing these strategies effectively, logistics companies can minimize the negative impact of nonconforming products, optimize their operations, protect their reputation and ensure customer satisfaction.
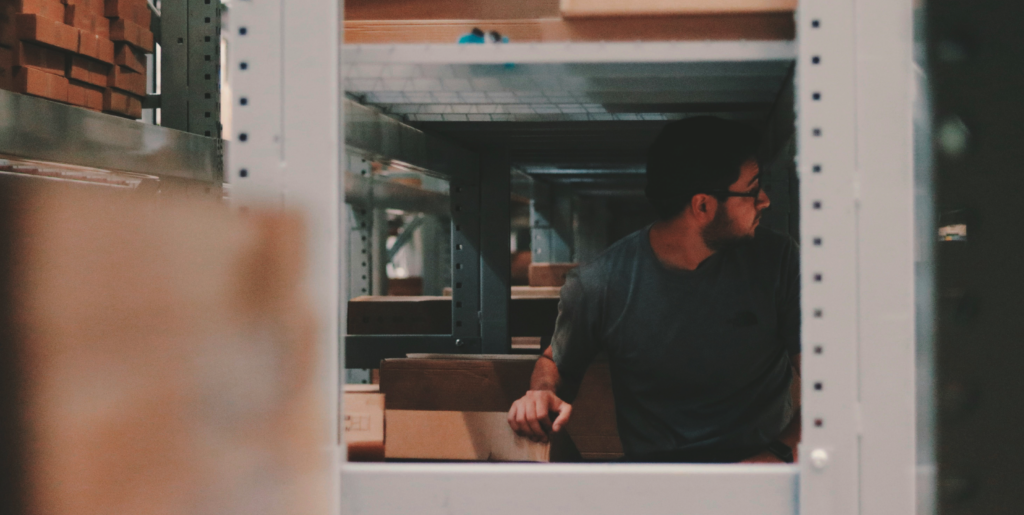
How to control non-conforming product outputs?
The control of outgoing non-conforming products in a logistics warehouse is a crucial process to prevent these products from reaching the end customer and causing problems such as returns, complaints and even damage to the company's image. Below we will see some important points about their treatment:
1. Establish rigorous exit controls:
- Pre-departure inspection: Implement a thorough inspection process before any product leaves the warehouse. This inspection should include verification of associated documentation, physical condition of the product and compliance with all established quality requirements.
- Use identification technology: Implement automatic identification systems, such as barcodes or RFID, to track and monitor the movement of nonconforming products within the warehouse. This will allow better traceability and real-time control.
- Establish exit control points: Designate specific control points in the warehouse where the final inspection of products is carried out prior to their exit. At these points, it should be verified that nonconforming products are not included in the shipments.
2. Implement authorization procedures:
- Establish authorization levels: Clearly define which individuals have the authority to authorize the release of nonconforming products from the warehouse. This may include warehouse managers, quality supervisors or personnel specialized in nonconforming product management.
- Document authorizations: Record in writing all authorizations for the release of nonconforming product. This documentation should include the identification of the product, the reason for the nonconformity, the number of units affected, the person authorizing the release and the final destination of the product.
3. Implement segregation measures:
- Separate storage: Store non-conforming products in a separate, secure area within the warehouse, clearly marked and with restricted access. This will prevent them from being mixed with compliant products and dispatched in error.
- Visible labeling: Clearly label nonconforming products with visible and distinctive labels indicating their condition. This will alert warehouse personnel and carriers to the special nature of these products.
4. Define specific output channels:
- Establish dedicated transport routes: Use specific transport routes for non-conforming products, different from those used for conforming products. This will help minimize the risk of errors and confusion during transport.
- Select reliable carriers: Work with reliable carriers that are experienced in handling nonconforming products and have the proper procedures in place to ensure their safe and uneventful transport.
5. Implement follow-up controls:
- Shipment tracking: Track shipments of non-conforming products from the time they leave the warehouse to their final destination. This will allow you to monitor their location and ensure that they arrive at the right place.
- Delivery Documentation: Require carriers to provide detailed documentation of the delivery of nonconforming products, including the date, time, signature of the recipient and condition of the product at the time of delivery.
6. Conduct periodic audits:
- Audit control procedures: Conduct periodic audits of non-conforming product output control procedures to verify their effectiveness and identify areas for improvement.
- Analyze output data: Analyze historical non-conforming product output data to identify trends, patterns and areas of risk.
- Implement corrective actions: Implement corrective actions based on the results of audits and data analysis to continuously improve the output control processes.
By implementing these strategies effectively, logistics companies can minimize the risk of non-conforming products leaving the warehouse and reaching the end customer, thereby protecting their reputation, reducing costs and ensuring customer satisfaction.
At ABC Logistics we integrate and implement many of these strategies in the storage of our clients ' merchandise , with the sole purpose of offering quality service and adding value to their business.